Global positioning system (GPS) technology has become virtually ubiquitous in recent years—affecting nearly every industry you can name in some way. The construction industry is no exception. Whether you need to track construction equipment, people, or other assets on the jobsite, GPS can be a major help.
But, what do construction companies use GPS tracking for? How does GPS control construction equipment use?
Construction Equipment Theft Statistics to Know
Before delving into the use of GPS tags on construction equipment, it’s important to know some basic facts about said equipment—especially the theft risks that construction equipment faces. Here are a few key facts about construction equipment theft to know:
- Global Market Size. According to Statista, the global construction equipment market in 2020 was valued “at around 113 billion U.S. dollars.”
- Total Thefts Reported. In the National Equipment Register’s (NER’s) 2016 Annual Theft Report (the most recent report available as of February 2021), there were 11,574 theft reports made to the National Crime Information Center (NCIC) regarding equipment theft in 2016 (including non-construction equipment, like riding mowers and garden tractors).
- Value and Mobility. Also according to the NER report, the key factors that determine the type of equipment that thieves are most likely to steal are “value and mobility.” Smaller, high-value assets that can easily be loaded onto a trailer are much more likely to be stolen than larger assets that are more difficult to move and don’t have as much value.
- Most Stolen Construction Equipment. Of the types of construction equipment reported stolen, loaders (skid steers, backhoes, and wheel loaders) are the most frequently stolen—second only to landscaping equipment like riding mowers and garden tractors.
- Annual Cost of Equipment Theft. The National Insurance Crime Bureau (NICB) estimates that the annual cost of equipment theft is “currently estimated to range from $300 million to $1 billion.” The fact that much theft goes unreported is what makes the range for the estimate so large.
Despite the bleak statistics concerning heavy equipment theft, fleet and asset managers do have one advantage on their side: construction GPS tracking. This is why GPS for construction equipment is so commonly used as a theft prevention and asset recovery measure.
What Is GPS for Construction Equipment?
GPS for construction equipment is a combination of hardware and software that you can use to track the locations of your most valuable and high-risk construction equipment. It uses GPS tracking devices that communicate with a satellite system in orbit to track the GPS tag’s location.
Each GPS tag communicates with several satellites at once to triangulate its current position whenever it “checks in” to report its location. The more satellites the GPS tracker can communicate with, the more accurate the positioning report is. And, the more frequently the GPS tag makes a report, the closer it can be to showing the tagged asset’s position in real time for construction site asset managers.
The software that is used with a GPS tracking device helps to organize the information transmitted by the device for asset managers to use more easily—doing things like recording the device’s location history, sending alerts when the device leaves a certain boundary, and more, depending on the software. It’s important to note that GPS software capabilities can vary from one tracking company to the next, so it’s important to check with the vendor to see what their specific software can do.
What Do Construction Companies Use GPS Tracking For?
Construction companies (and rental companies servicing construction industry clientele) can use construction GPS tracking equipment in a variety of ways that help to save money and reduce risk.
Some key GPS construction applications include:
1. Construction GPS Tracking and Theft Prevention
Whether you rent heavy construction equipment out to third parties or your organization owns heavy equipment that your in-house team uses, GPS for construction equipment is an issue that affects not only your bottom line but your operations as well. In addition to the cost of replacing stolen construction equipment, you also have to contend with the downtime in your operations that results from having equipment missing from your inventory.
Your heavy construction equipment is exposed to numerous risks—these risks are amplified when equipment is being used off-site or left alone after hours. This equipment is expensive and valuable, which can make it a target for vandalism and theft. But how are you supposed to keep an eye on your heavy construction equipment when no one is physically around to look after it?
Using an effective GPS construction equipment tracking system is one way to help solve this costly concern. Heavy equipment tracking is essential for tracking the locations of your large construction assets anytime, anywhere. One of the most effective ways to achieve this is through the use of a heavy equipment tracking device—particularly in combination with geofencing technology.
Setting Boundaries with Geofencing Tools
A geofence is a tool in the Rastrac software dashboard that allows you to outline virtual boundaries that correspond to real-world geographic locations. Geofencing enables you to create multiple geofences — as well as geofences within geofences — around areas that you wish to closely monitor, such as high crime areas, jobsites, equipment storage lots, and office parking lots. These boundaries can be designed into a variety of standard and customizable configurations to fit the area you wish to monitor.
If you set a geofence around a jobsite, you’ll receive an instant, automated alert whenever a piece of tagged heavy construction equipment either enters or leaves that boundary. This capability helps you to increase your equipment theft prevention efforts and keep your machinery safe all year long.
Using Automated Alerts to Improve Theft Prevention
Rastrac’s construction equipment tracking software uses GPS technology to remotely monitor your equipment and their locations, as well as send automated alerts for specific functions. These notifications can be programmed to send alerts for a variety of different events.
If you receive a notification indicating that your equipment has moved, there is a way to help prevent it from disappearing. Some Rastrac tracking devices are capable of using a starter disabler function. Although this function will not stop an active vehicle that is currently in operation, the next time someone tries to activate the starter, the disabler will prevent it from starting.
2. GPS Construction Equipment Location Tracking for Remote Site Management
Some construction site managers use GPS simply as a tool for remotely monitoring and managing their construction sites. With GPS trackers for construction equipment, site managers can verify where their gear is on the jobsite from anywhere they can access the internet.
For example, say a big crane is supposed to be on the north side of the jobsite to efficiently offload heavy items from a trailer in the loading zone that the site’s forklifts can’t handle. However, the GPS shows it’s in the southwest corner. Armed with the GPS data, you can call the crew up and let them know that the crane needs to be moved (or at least get an explanation of why the asset is out of place).
Without GPS, you would have to be onsite to see the out-of-place equipment or else risk delays because nobody thought to tell you about the crane getting moved.
3. Improving Contract Enforcement for Rented Equipment
Whether your company is the one that owns and is renting out heavy construction equipment or you’re relying on heavy equipment rentals to get the job done, asset tracking can keep both owners and renters accountable. By having access to data that pinpoints the exact current location of a piece of machinery as well as all of its previous locations, you can ensure that it is staying within the area agreed upon in the rental contract.
Geofencing can also be a valuable solution for contract enforcement of heavy equipment rentals. It allows you to set up alerts that notify you whenever a GPS-tagged asset has left the determined service area. This means you’ll always know where the assets are, effectively helping to prevent contract breaches.
If one party believes there is a discrepancy, it doesn't have to be a “he-said-she-said” argument—you can simply look over the historical GPS tracking data to determine exactly where a piece of equipment was at a certain time and if it ever left the site parameters.
4. Optimizing Maintenance for Construction Equipment
Want to know that your equipment is in good operating condition and is safe for an operator to handle? With GPS construction equipment tracking and monitoring, you and your employees can rest assured knowing that your equipment is running in as safe a condition as possible.
A GPS tracking device for equipment is installed on each of your machines or vehicles, allowing you to tap into its onboard diagnostics system. The GPS construction telematics reporting enables you to get accurate and up-to-date reports about the conditions of your assets, as well as receive alerts via fault codes when something is wrong.
With automated GPS construction tracking solutions, you can:
- Identify what equipment is spent idling at jobsites and how often,
- Determine what regular preventative maintenance services need to be performed, and
- Monitor fuel usage and engine idle times to reduce costs and enhance project management.
5. Improving Employee Safety
It’s obvious that unsafe driving habits not only leave your employees at risk, they put your assets—and the community at large—at risk as well. The equipment at jobsites isn’t always limited to construction equipment. It also can include heavy equipment trucks and vehicles that may travel around the location or travel to and from it to transport materials and supplies.
As a construction fleet or site manager, you want to trust that your employees are doing the right thing when behind the wheel. However, it’s imperative to know for certain how safely and professionally your employees are operating those vehicles. With GPS for construction vehicles, you can monitor a variety of information, including:
- Driving speeds,
- Acceleration and braking rates,
- How frequently and quickly the vehicle turns, and
- Fuel usage and idle times.
To learn more about the uses of GPS technology for construction equipment tracking and how it can provide greater visibility into all aspects of your fleet, check out our GPS construction tracking feature sheet.
If you have additional questions about the uses of GPS construction technology for asset management, get some help from the fleet and asset management experts at Rastrac today.
Like what you're reading? Subscribe to our blog.
Get our latest posts straight to your inbox.
Subscribe to Our Blog
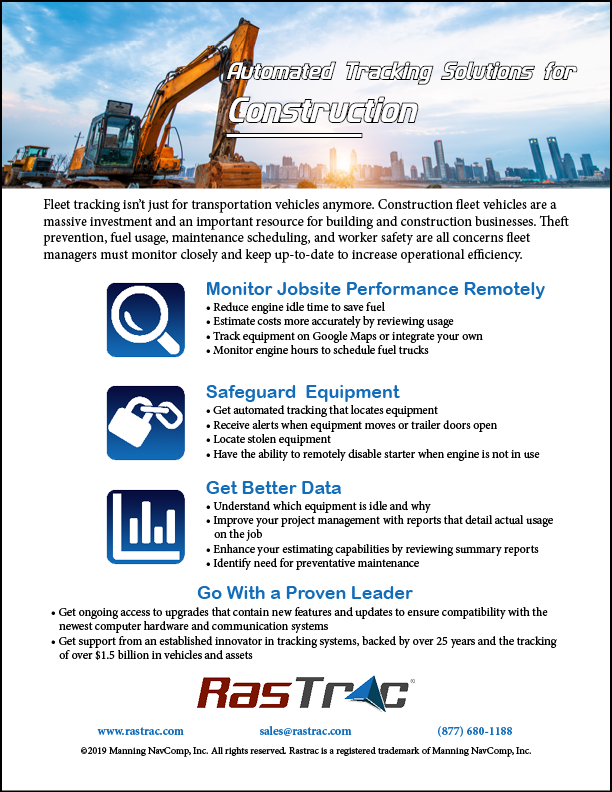
Automated Tracking Solutions for Construction
Download the feature sheet
Download Now